In the heat of summer, a functioning car AC system can be your ultimate relief from the sweltering temperatures. However, there are moments when the cooling embrace of your vehicle’s air conditioning seems to slip away, leaving you in discomfort. One of the most common issues that drivers encounter is the dreaded “AC compressor not engaging” scenario. When the heart of your car’s AC system, the AC compressor, fails to kick into action, the entire cooling process comes to a screeching halt. In this guide, we delve into the intricacies of troubleshooting a car AC compressor that refuses to turn on. From unraveling the components of the AC system to understanding the potential culprits behind this issue, we’ll equip you with the knowledge needed to diagnose and address this cooling conundrum. Whether you’re a seasoned car enthusiast or a casual driver, our exploration of AC system troubleshooting will empower you to restore the chilly comfort your journeys demand.
Understanding the Role of an AC Compressor in Vehicle Cooling Systems
In the intricate web of components that comprise a car’s HVAC (Heating, Ventilation, and Air Conditioning) system, the AC compressor stands out as a pivotal player. For many, the mechanism behind the burst of cool air on a sweltering day remains a mystery. Yet, at the heart of this cooling wonder is a complex interplay of physics and engineering.
As vehicles traverse the roads, they are constantly drawing in external air. This air, laden with varying degrees of heat and moisture, is far from the ideal temperature passengers might desire. Here’s where the HVAC system and, more specifically, the AC compressor step in.
The AC compressor is essentially the heart of the air conditioning system. It is tasked with regulating and circulating a special fluid known as a refrigerant. This refrigerant, under specific pressures and temperatures, has the remarkable ability to absorb and carry away heat.
In simple terms, as the outside air is ushered into the HVAC system, the refrigerant, under the AC compressor’s guidance, captures the heat from this incoming air. Once the refrigerant has become saturated with this absorbed heat, the compressor ensures it is channeled away, making room for a new batch of unsaturated refrigerant to continue the cooling process.
A malfunctioning compressor can disrupt this well-orchestrated process. Without the compressor effectively circulating the refrigerant and regulating its flow, the air would retain a significant amount of its original heat, leading to tepid or even warm air from the vents. Thus, while the AC compressor might be just one component among many, its role is undeniably crucial in ensuring that vehicles offer a refreshing oasis even on the hottest of days.
Why Might an AC Compressor Fail to Activate?
A car’s air conditioning system plays a pivotal role in ensuring comfortable temperatures inside the vehicle. At the heart of this system is the AC compressor. This component essentially has two operational states: active (engaged with the drive belt) or inactive (disengaged). When the AC compressor fails to activate, pinpointing the exact cause requires systematic troubleshooting.
Here’s a deeper dive into potential culprits and diagnostic steps:
1. Location of the Problem: Electrical Circuit or Compressor?
Before delving into detailed troubleshooting, it’s imperative to discern if the issue lies within the AC’s electrical circuit or directly with the compressor. This distinction aids in narrowing down potential causes.
2. Inspecting the AC Electrical Circuit:
- Fuses: One of the primary causes of AC failure could be a malfunctioning fuse. A blown fuse disrupts power flow, causing the compressor to remain inactive. Regularly inspecting and replacing defective fuses can remedy this;
- Pressure Switch: The AC system relies on an optimal balance of refrigerant pressure. The pressure switch monitors these levels. If refrigerant pressure strays too high or low, it risks compromising the system’s integrity. Thus, the switch will disengage the compressor as a safeguard. Faulty switches might yield inaccurate readings, leading to unnecessary compressor shutdowns. Replacement of malfunctioning switches can resolve this issue;
- Refrigerant Levels: Adequate refrigerant is essential for the compressor’s operation. Insufficient levels can cause the compressor to halt. Periodic checks and top-ups can ensure the refrigerant remains at optimal levels;
- WOT (Wide Open Throttle) Connectivity: Some vehicles incorporate protective mechanisms like the WOT switch, which links the AC system to the car’s throttle. Consulting the vehicle’s workshop manual can provide insights into such connections and potential issues that might affect compressor activation;
- Relay Systems: Modern cars often use relay boxes, which serve multiple purposes, from controlling engine cooler fans to managing the compressor clutch. These boxes can be vulnerable to damage, which in turn can disrupt various connected systems, including the AC. Ensuring the relay box’s functionality is crucial;
- Wiring and Connectivity: Electrical systems, especially in older vehicles, can deteriorate over time. Checking for signs like burnt cables, corroded contacts, loose connectors, and other anomalies can prevent unwanted AC compressor interruptions.
In conclusion, a non-operational AC compressor can be attributed to a myriad of causes. Regular maintenance and vigilance can ensure early detection and rectification of these issues, ensuring a comfortable driving experience.
Identifying and Addressing Compressor Issues
1. Compressor Clutch Engagement Issues:
The compressor acts as the heart of a vehicle’s air conditioning system, and any issues with it can lead to further complications. One common problem is when the compressor gets jammed. In this situation, although the clutch attempts to engage, it may not successfully do so and could begin to slip. Over time, this slippage can lead to overheating and even potential burnout of the clutch. Moreover, it can cause damage to the compressor’s coil. Consequently, it becomes imperative to either repair the compressor or consider a full replacement to avoid escalating damage.
2. Potential Magnetic Coil Wiring Defects:
The compressor’s magnetic coil wiring is another vital component that can sometimes malfunction. A practical method to assess the condition of the coil wiring is to perform a continuity test. This test measures the resistance between the two terminal ends of the coil. Should the circuit display an open condition, it is indicative of a break or cut within the coil wiring. When faced with such a scenario, replacing the magnetic coil is often the recommended course of action. This is mainly because replacement tends to be more cost-effective than pursuing repairs, especially in the long run.
3. Reasons Behind Compressor Clutch Slippage:
Slippage in the compressor clutch can arise due to various reasons, each warranting attention:
- Oil Leakage: The presence of oil on the clutch disc can drastically reduce its efficiency. When oil seeps into this area, it makes the clutch slippery. As a result, there’s insufficient friction generated to drive the compressor’s inner pulley efficiently. Addressing oil leakage is vital not only for the clutch but also for the overall health of the vehicle’s air conditioning system;
- Worn-Out Clutch Disk: Much like any other mechanical component, the clutch disk in a compressor is subject to wear and tear. Over time, due to constant engagement and disengagement, the disc can become worn out. A deteriorated clutch disk can hamper the seamless movement of the compressor. In cases where the clutch assembly has been compromised, whether by oil contamination or wear, it’s advisable to opt for a complete clutch assembly replacement. This ensures the compressor operates at its peak efficiency and prolongs its life span.
Guide on AC Compressor Removal
1. Serpentine Belt Detachment:
Before beginning the removal process, it’s essential to relieve the tension from the serpentine belt. This belt often connects multiple components, including the AC compressor. By using an appropriate tool, like a serpentine belt tool, gently release the pressure from the belt tensioner, allowing the belt to be removed safely.
2. Clearing the Work Area:
The AC compressor may have various components surrounding it. It’s crucial to ensure these components are safely and efficiently removed to access the compressor. A complete socket set is recommended for this step, as most of the bolts and nuts can be loosened and removed with it.
3. Line Disconnection:
After clearing the surrounding area, proceed to disconnect the lines linked to the AC compressor. It’s vital to protect these lines from contamination and ensure no refrigerant escapes. For this purpose, tightly insert a clean cloth or rag into the open lines, forming a secure seal.
4. Detaching the Compressor:
With everything out of the way, locate the mounting bolts that hold the compressor in place. Unscrew these carefully, and once all are removed, the compressor can be safely lifted and removed from its position.
Guide on Compressor Clutch Replacement
1. Preparing the Compressor:
Lay the compressor on a soft cloth or padding. This precaution ensures the compressor doesn’t get scratched, damaged, or contaminated by resting directly on a rugged or dirty surface.
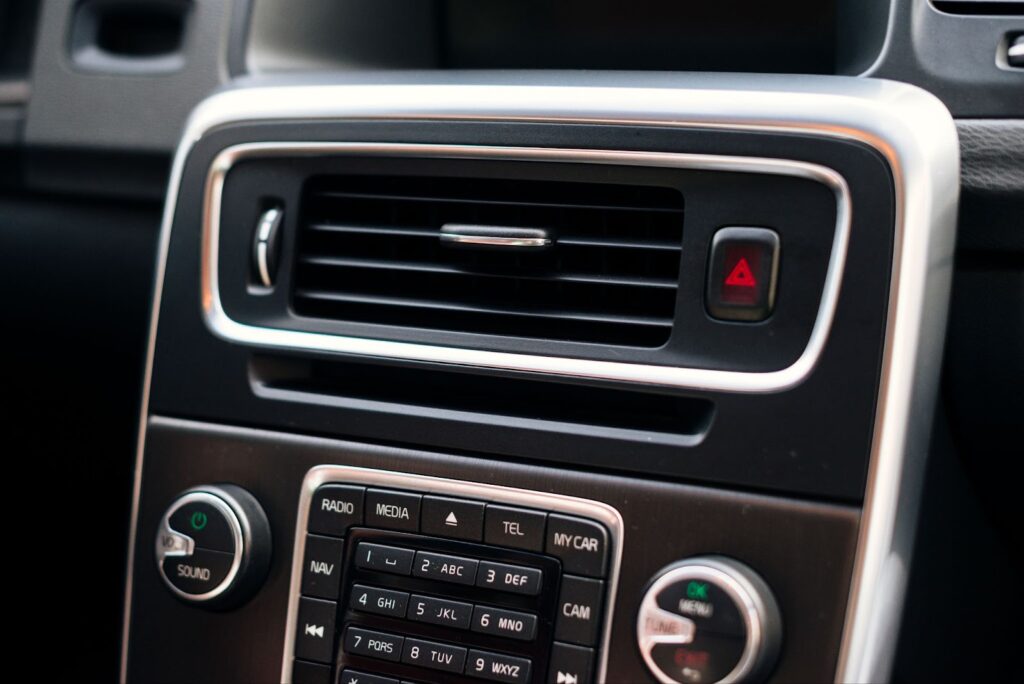
2. Removing the Central Bolt:
The clutch pulley’s center has a tightly secured bolt. Due to the tightness, this bolt may require substantial effort to remove. It’s advisable to have an assistant stabilize the compressor while working on this bolt to prevent any accidental slips or movements.
3. Clutch Disc Removal:
Once the central bolt is out, the clutch disc can be carefully pried off.
4. Accessing the Pulley:
On the central axle, there’s a rubber bushing. Carefully remove this. Then, using a pair of sturdy pliers, detach the retention clip that keeps the pulley in place. Remember, this clip can be under pressure, so wearing safety glasses or eye protection is essential to prevent any potential injuries.
5. Unveiling the Electromagnetic Segment:
After removing the pulley, the electromagnetic component of the clutch becomes accessible. Another retention clip typically holds this part. With caution, remove this clip, enabling the removal of the electromagnetic section.
6. Reassembling the Clutch:
Once the old parts are removed, it’s time to assemble the clutch using the new components and retention clips provided. Ensure each part fits snugly and securely, ensuring the longevity and efficiency of the newly assembled clutch.
Conclusion
In conclusion, addressing air conditioning problems, particularly when the car AC compressor is not turning on, necessitates a systematic AC system diagnosis. A malfunctioning AC compressor can lead to discomfort, decreased fuel efficiency, and potential damage to other components. Through a step-by-step assessment, starting with checking electrical connections, fuses, and relays, followed by evaluating refrigerant levels and pressure, and inspecting the compressor clutch, drivers can effectively identify the root cause of the issue. Regular maintenance, including cleaning debris from the condenser and maintaining proper refrigerant levels, can also contribute to the longevity and optimal performance of the AC system. By staying vigilant and informed about these diagnostic steps, individuals can ensure a cool and comfortable driving experience, even during the hottest of days.